Adaptable for: Silk, Rayon, Cotton, Jute, Asbestos, etc
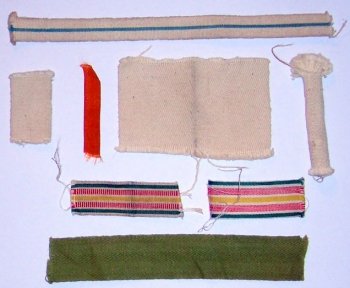
For the Manufacture of: Ribbons, Petershams, Galloons,
Gimps, Tapes, Elastics, Webbings, Listings, Spindle Tapes
|
The Haywood Patent Narrow Fabric Loom has been evolved as a result of
over ten years' research, owing to the admitted fact that the ordinary
type of smallware loom is far from being a really satisfactory machine.
In many respects it is entirely original in design and contains a number
of features which are rotected by patent, not only in England, but in all
European countries and the U.S.A.
An outstanding fature of this Narrow Fabric Loom is its all-metal
construction, including the shuttle. It is made in comparatively small
sections each of which is a complete unit. Two, three or more sections
can be coupled together and driven from a common source if so desired.
For the execution of small orders the advantage of a unit with few spaces
is apparant.
The Loom is designed to weave material from 1/2 in wide up to 2 in wide
and the number of shuttle in the standard section is as follows:
For material 0.5 in wide 12 shuttles
1.0 in 9
1.25 8
1.5 7
2.0 6
|
The Haywood Loom is particularly suitable for weaving silk and artificial
silk ribbons, but is equally efficient upon all classes of goods which
fall within its capacity, an example being the weaving of spindle
tapes for ring spinning and ring doubling frames.
The shuttle mechanism is by means of rack and pinion the basis of
the reciprocating motion being a fabroil rack gearing with cut steel pinions
The Beat-up Motion is a patent feature of the loom. The effect of
the arrangement is to give the slay an unusually long dwell in order to
allow the shuttles ample time to cross the shed, without fear of catching
the warp threads and, at the other end of the stroke, to give a rapid
beat-up blow.
The Heald Frames and Healds are also of all-metal construction and
particular attention has been devoted to the shedding cams so that smooth
changing of the warp threads is ensured even when running at high speeds.
A most efficient Let-off Motion is employed on the Ribbon and Tape
Looms embodying a patent compensating motion which ensures an even tension
by self-adjustment when stress is put upon the warp threads during the
changing of the shed.
The Take-up Roller is driven through a double clutch arrangement
and simply by altering the position of a link which connects the beat-up
arm to the lever actuating the take-up motion itself, any desired number
of picks per inch from 20 to 120 can be obtained without the employment
of change wheels. According to class of material to be woven, the take-up
roller may be covered with abrasive or cloth or knurled upon the surface.
The loom is driven by means of a single pulley through a constantly
revolving shaft. It is stoped and started by means of an efficient cone
friction clutch which is thrown out of gear by the patent automatic
Weft Stop Motion whenever a weft thread breaks or a spool runs empty
A Warp Stop Motion can be applied when desired, which also acts
upon the clutch in a similar manner. The loom is restarted instantaneously
by a slight depression of the friction lever.
Dobby. The shedding mechanism is by means of cams up to 8 shafts,
but the standard loom can be arranged for dobby control, the dobby being
placed either above the loom or on the side as illustrated in Fig 3
where floor space is not of vital importance.
Jacquard. For patterned ribbons outside the capacity of the dobby
a double lift Jacquard can be fitted above the loom as shown in Fig 1 and
driven by simple connections to the standard mechanism.